HYDRAULIC IRONWORKER MACHINES
HlW- 55 ~ HlW- 220
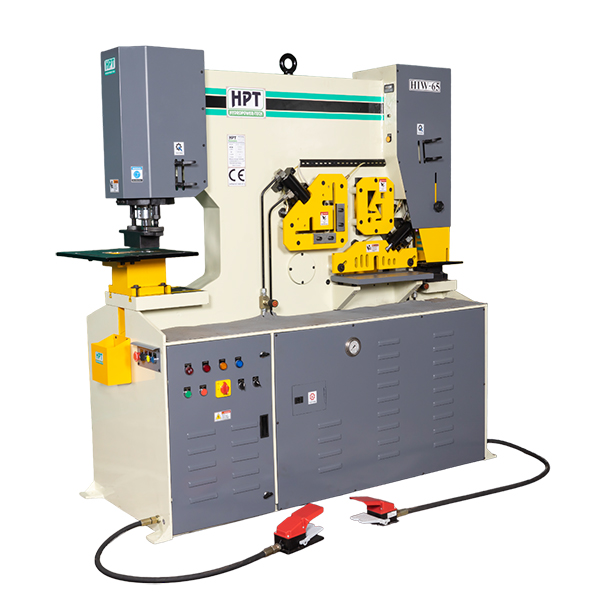
Hydraulic Ironworker Machines
Ironworker Machine is a versatile and powerful piece of equipment used in metalworking and fabrication. It’s designed to cut, punch, shear, and bend different types of metal materials. Ironworker machines are commonly used in industries such as construction, metal fabrication, and manufacturing, where precise and efficient metalworking is required.
Some key features and capabilities of an Ironworker machine may include:
- Punching: Ironworkers can punch holes of various sizes and shapes into metal sheets and plates. They typically have a selection of punch dies that can be interchanged based on the required hole size and shape.
- Angle Cutting: Some models of Ironworker machines are equipped with an angle cutting station, allowing precise cutting of angles and various profiles.
- Section And Bar Cutting: Ironworkers can cut C Section, I Section, round and square bars, as well as rod stock, using specialized cutting tools.
- Flat Shearing: The machine can cut metal sheets and flat bars using a shear blade. This allows for straight and clean cuts.
- Notching: Ironworkers may include a notching station to create notches and cutouts in metal pieces, which is often useful for connecting components.
- Bending: Ironworker machines have bending attachments to bend metal bars, plates, and angles to specific angles and shapes.
- Customization: Different Ironworker models come with varying capabilities, allowing manufacturers to choose the machine that best suits their production needs.
Safety is crucial when working with Ironworker machines due to their high force and potential hazards. Proper training and adherence to safety guidelines are essential for operators.
Manufacturing Ironworker machines involves engineering, fabrication, and quality control processes to ensure their efficiency and reliability. As a manufacturer, you may need to consider market demand, competition, and customer requirements when designing and producing your Ironworker machines.
TECHNICAL SPECIFICATIONS :
Perticular | HIW – 55 | HIW – 65 | HIW – 85 | HIW – 110 | HIW – 110 EX | HIW – 135 | HIW – 165 | HIW – 220 |
Punching | ||||||||
Punching Pressure | 55 Ton | 65 Ton | 85 Ton | 110 Ton | 110 Ton | 135 Ton | 165 Ton | 220 Ton |
Punch Capacity (Diameter x thickness) | 22 x 16 | 22 x 20 | 30 x 20 | 30 x 25 | 30 x 25 | 33 x 28 | 36 x 32 | 40 x 38 |
45 x 8 | 50 x 9 | 50 x 12 | 50 x 15 | 50 x 15 | 50 x 18 | 50 x 23 | 50 x 30 | |
Throat Depth in S/SD Model | 275 / – | 310 / 510 | 310 / 510 | 310 / 510 | 310 / 510 | 570 / – | 570 / – | 570 / – |
Maximum Stock Length | 100 | 100 | 100 | 100 | 100 | 100 | 100 | 100 |
Cycle/ Min. (20mm Stroak) | 25 / 32 | 20 | 21 | 21 | 21 | 20 | 25 | 25 |
Working Height up to die | 910 | 910 | 950 | 950 | 950 | 1020 | 1050 | 1050 |
Flate Shearing | ||||||||
Flate Bar Shear (Width x Thickness) | 300 x 12 | 350 x 15 | 460 x 15 | 610 x 16 | 610 x 16 | 610 x 18 | 760 x 20 | 700 x 25 |
240 x 16 | 240 x 20 | 300 x 20 | 400 x 20 | 400 x 20 | 400 x 25 | 400 x 30 | 425 x 30 | |
Blade Length | 310 | 360 | 465 | 620 | 620 | 620 | 770 | 720 |
Angle flange Trim | 65 | 75 | 100 | 100 | 100 | 100 | 120 | 120 |
Working Height | 820 | 920 | 920 | 950 | 950 | 950 | 950 | 950 |
Angle Shearing | ||||||||
Angle 90 Shearing | 100 x 100 x 10 | 130 x 130 x 13 | 152 x 152 x 13 | 152 x 152 x 15 | 152 x 152 x 15 | 152 x 152 x 18 | 200 x 200 x 20 | 200 x 200 x 20 |
Angle 45 Miter Shearing | 50 x 50 x 6 | 65 x 65 x 8 | 80 x 80 x 10 | 80 x 80 x 10 | 80 x 80 x 10 | 80 x 80 x 10 | 80 x 80 x 10 | 100 x 100 x 10 |
Working Height | 1080 | 1150 | 1150 | 1150 | 1150 | 1160 | 1160 | 1160 |
Section & Bar Shearing | ||||||||
Round Bar Shearing | 32 | 40 | 50 | 50 | 50 | 50 | 60 | 70 |
Square Bar Shearing | 32 x 32 | 38 x 38 | 50 x 50 | 50 x 50 | 50 x 50 | 50 x 50 | 60 x 60 | 60 x 60 |
Channel Shearing | 125 | 152* | 180* | 180* | 200* | 200* | 250* | 300* |
I Beam Shearing | 125 | 152* | 180* | 180* | 180* | 180* | 200* | 300* |
Working Height | 1150 | 1300 | 1300 | 1315 | 1315 | 1315 | 1375 | 1375 |
Notching | ||||||||
Rectangular (W x D x T) | 50.8 x 90 x 6 | 50.8 x 90 x 9 | 50.8 x 90 x12 | 63.5 x 90 x 12 | 63.5 x 90 x 12 | 63.5 x 90 x 13 | 63.5 x 90 x 16 | 63.5 x 90 x 18 |
Vee-Notcher (Side x Side x T) | 80 x 80 x 6 | 90 x 90 x 8* | 90 x 90 x 10* | 105 x 105 x 12* | 105 x 105 x 12* | 105 x 105 x 13* | 105 x 105 x 16* | 105 x 105 x 16* |
Large V-Notcher (Side x Side x T) | – | 145 x 145 x 8 | 145 x 145 x 10 | 145 x 145 x 12 | 145 x 145 x 12 | 145 x 145 x 13 | 145 x 145 x 13 | 145 x 145 x 15* |
Working Height | 850 | 850 | 860 | 860 | 860 | 860 | 920 | 920 |
Optional Tooling | ||||||||
Single V Press Break (W x T) | 250 x 10 | 250 x 15 | 250 x 15 | 250 x 20 | 250 x 20 | 250 x 20 | 250 x 20 | 250 x 20 |
Multi V Press Break (W x T) | 400 x 5 | 500 x 5 | 500 x 5 | 700 x 5 | 700 x 5 | 700 x 5 | 700 x 6 | 700 x 6 |
Angle Bending | 76 x 6 | 102 x 6 | 102 x 8 | 102 x 13 | 102 x 13 | 102 x 13 | 102 x 13 | 102 x 13 |
Pipe Notcher (Dia.) | 114 | 114 | 114 | 114 | 114 | 114 | 114 | 114 |
Other | ||||||||
Electric Power (HP) | 7.5 HP | 7.5 HP | 10 HP | 10 HP | 10 HP | 15 HP | 20 HP | 25 HP |
Net Weight (Apr.) S / SD | 2300 / 2300 KG | 2600 / 3100 KG | 2950 / 3250 KG | 3600 / 3900 KG | 3950 / 4200 KG | 5200 KG | 6500 KG | 7800 KG |
Machine Dimentation (L x W x H) | 1750 x 750 x 1800 | 1970 x 800 x 2000 | 2100 x 820 x 2060 | 2340 x 860 x 2110 | 2400 x 920 x 2150 | 2420 x 980 x 2150 | 2550 x 1050 x 2150 | 2700 x 1200 x 2250 |
Our Product Live in Action :
If you have any specific questions or need more information related to manufacturing Ironworker machines, feel free to ask!